Electrolyzers
Electrochemically activated solutions (ECA solutions) – anodic (anolyte) and cathodic (catholyte) fractions, with physical-chemical parameters changed to the extent possible, generated in special electrochemical systems (ECA devices) as a result of electrolysis of initial solution or water at diluted salt conversion rate close to theoretically possible.
In the course of development of electrochemical activation during several decades the following indispensable conditions of generation of electrochemically activated solutions have been selected and stated.
Necessary technical conditions for generating ECA solutions |
|||
---|---|---|---|
1) | unipolar electrochemical action | ![]() |
separation of anode and cathode chambers of the electrolyzer with a membrane or diaphragm; |
2) | electrochemical treatment of maximum possible amount of microvolumes of liquid in high intensity electric field on the electrode surface | ![]() |
optimal structure and arrangement of electrodes (coaxially-arranged electrodes); |
3) | maximum production rate of oxidants in anode chamber and reducing agents in cathode chamber of the electrolyzer in the absence of migration of ions of coating and electrodes destruction | ![]() |
selection of electrode coating and material; |
4) | maximum conversion rate of diluted salts of initial solution | ![]() |
structurally assured possibility of short time of electrochemical exposure of the liquid (0.3 – 10.0 seconds) at considerable current density up to 3000 A/m2, voltage up to 3000 mV and low specific power consumption from 0.05 to 5.0 Wхh/l; |
5) | adjustment of composition of active compounds in anolyte (from hypochloric acid to hypochlorite ions) and catholyte, as well as their physical and chemical parameters depending on process requirements | ![]() |
ceramic diaphragm, separating anode and cathode chamber, providing the necessary pressure differential and migration of selective ions; |
6) | possibility to remove by-products of electrolysis, heavy-metal ions and foreign substances to drainage system | ![]() |
flow-through electrolyzer design; |
7) | possibility to use solutions of various mineralization, from fresh drinking water to brines | ![]() |
combination of design features, electrode and diaphragm materials, and know-how. |
Know-how and design features of flow-through modular electrochemical reactors developed by Vitold M. Bakhir, which have evolved from electrolyzer with plate electrodes (1970s) to a line of advanced electrochemical reactors (2012) used in various processes, enable the generation of low-mineralized solutions with high oxidant concentration of over 500 mg/l and mineralization 0.5 g/l. Why is it so important?
Stages of development of technical electrochemical systems for electrochemical activation
Stage 1 (1972 – 1974) |
Development of flow-through electrochemical reactors with plate electrodes separated with a diaphragm |
Stage 2 (1974 – 1984) |
Development of flow-through electrochemical reactors with coaxially arranged electrodes separated with a diaphragm |
Stage 3 (1985 – 1989) |
Development of flow-through electrochemical reactors with coaxially arranged electrodes separated with a diaphragm as monoblock units |
Stage 4 (1989 – up to present) |
Development of flow-through electrochemical reactors with coaxially arranged electrodes separated with a diaphragm; selection of optimal dimensions and materials |
Flow-through electrochemical reactors with plate electrodes
The first stage of ECA
![]() |
Developed in 1972-1974, devices with plate electrodes proved their efficiency and prospectiveness in gas and oil industry. The electrodes were used for disinfection of large volumes of drill mud and strata water with mineralization of 10-20 g/l. |
Flow-through electrochemical reactors with coaxially-arranged electrodes separated with a diaphragm
The second stage of ECA
![]() |
In 1974-1984 it was decided to pass from plate electrodes to coaxially-arranged electrodes separated with a diaphragm. Those electrochemical reactors could be used much more extensively, as they could operate with solutions the mineralization of which was 3-5 g/l and higher. |
Flow-through electrochemical reactors with coaxially-arranged electrodes as monoblock units
The third stage of ECA
![]() |
In 1985-1989 devices for electrochemical activation of water and aqueous solutions were developed having monoblock reactors with built-in coaxially arranged electrodes separated with a ceramic diaphragm. That type of reactors could operate at significant pressure differential on the diaphragm. Technical and economic performance of those reactors was considerably improved with significant reduction of their weight and dimensions. |
Flow-through diaphragm electrochemical reactors with coaxially arranged electrodes
The fourth stage of ECA
![]() FEM-1 and FEM-3 elements |
In 1989 first flow-through electrochemical elements FEM were developed, as single elements with coaxially arranged electrodes separated with a diaphragm. The optimal selection of electrolyzers’ design and materials defined further development of that type of reactors. FEM elements have proven to be the most prospective as compared to previous types of reactors. From 1990 the technology of ECA development is based on the use of FEM elements, MB (modules of Bakhir) and reactors on their basis. |
![]() MB elements with diaphragms ? 11 mm ![]() MB elements with diaphragms ? 26-28 mm |
In 2009 improved types of FEM elements were developed – MB elements or Bakhir Modules. MB elements are multipurpose and can be used both with low-mineralized and concentrated solutions. |
![]() |
In 2010 activities on identifying lines of further improvement of MB elements were carried out, related to substantial increase of elements’ production capacity together with design simplification. |
![]() MB-100-01 and MB-700-01 |
In 2011 new models of MB elements were created, with higher production rate, reliability, longer service life, excellent maintainability, capacity to operate for a long time at high loads. Design and technological solutions were found ensuring long-term operation of the elements without parameters downgrading in water with high content of hardness salts, as well as design and technological solutions allowing to completely exclude the need to clean cathode chambers and elements’ diaphragms with acid. |
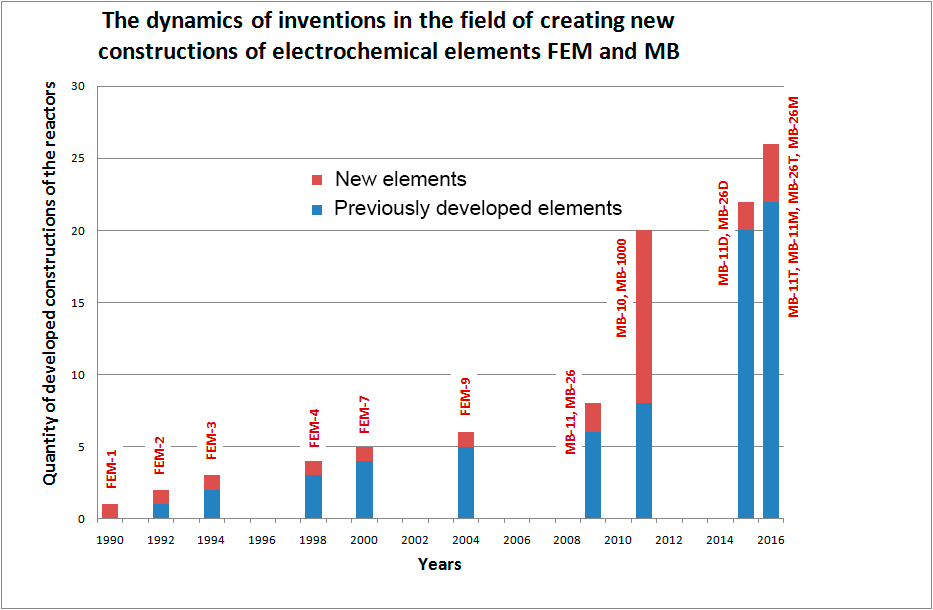